АЗОТИРОВАНИЕ СТАЛИ И ЧУГУНА – ПОВЫШЕНИЕ ТВЕРДОСТИ ДЕТАЛЕЙ
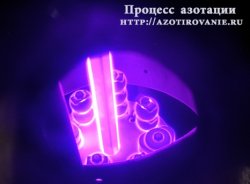
Но такие архаические техники были крайне длительные по времени и значительные по трудозатратам. Процесс изготовления одного клинка занимал многие месяцы. Поэтому уже в 19-м веке для упрочения показателей по твердости стальных деталей в условиях массового производства применялась закалка изделий. Суть ее заключался в том, что раскаленную до 700-800 градусов деталь окунали в воду или в масло и резко остужали там.
Такое резкое термическое падение температуры приводило к изменению кристаллической структуры детали и перераспределению в её объеме различных химических элементов, прежде всего углерода. И за счёт этого детали становились прочнее, тверже и износоустойчивее. Для производства клинков сабель и шпаг, или различного нехитрого сельхоз инвентаря, как и прочих стальных простых орудий труда, такие методики упрочнения вполне подходили. А вот с возникновением точного машиностроения оказалось, что при закаливании в массиве деталей при шоковом охлаждении возникают объемные термические напряжения, которые неравномерно распределены по объему детали и со временем начинают «выходить на поверхность».
И такие процессы ведут к изменениям геометрической формы точных деталей. Изменение размера даже в не небольших деталях могло достигать нескольких дестях долей миллиметра, а на крупных деталях – даже нескольких миллиметров… Т.е. для обработки точных деталей или элементов, которые потом собирались в четко рассчитанные механизмы со строгими допусками и посадами, такая методика закалки не годилась никак. Конечно, можно было в итоге после термообработки деталь отшлифовать в нужный размер.
- НО, во - первых: шлифовать твердый каленый металл- дело непростое, трудное и дорогостоящее;
- Во – вторых: термические напряжения могли «вылезть» и после шлифовки, через месяц, два или даже позже с момента термоупрочения.
В процессе развития металлообработки и систем упрочения металлов, стали появляться термо-химические способы упрочения. Они давали более прочные детали, и теоретически приводили к меньшим термическим искажениям размеров. Первой был создана цементация, процесс насыщения поверхностного слоя стальных деталей углеродом.
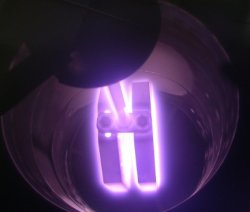
В первом десятилетии 20-го века в России была разработана технологии азотирования стали. Т.е. насыщения поверхностного слоя стали соединениями азота- нитридами. Это очень твердые и жесткие соединения. Азотирование в газовой среде происходило уже при 700-800 градусов С. Термические искажения при такой технологии были уже заметно меньше, чем при цементации или закалке. А в последних десятилетиях 20-го века начало активно развиваться ионно-плазменное азотирование в техническом вакууме. Подробности по технологии азотирования тут.
При этой технологии основную роль в соединении железа и азота играла не температура, а работа тлеющего электрического разряда на поверхности стальной детали. Поэтому и температура процесса составляет всего 500-550 градусов. При такой температуре нагрева практически нет термических искажений. Поэтому в современном машиностроении азотирование путем ионно-плазменного процесса оказывается самым эффективным способом упрочения поверхности стальных деталей.
11-11-2018, 17:10